How tyres are made
When you stick a new tyre on your vehicle you assume it’s done 0 km. Which is correct. It won’t have turned a rotation on a vehicle. But it will have already completed an impressive journey just to make it to you. The process they go through is really rather fascinating... and the starting point might just surprise you.
They Don't Just Grow on Trees You Know
Did your Mum ever say that to you? Well...when it comes to tyres they might not grow on trees but it is where their journey starts. The key raw ingredient in tyres is natural rubber. Actually, it’s latex. A white, milk like liquid that is extracted from the rubber tree, otherwise known as Hevea brasiliensis. Native in the Amzonian rainforests of South America, rubber trees are commercially grown and harvested throughout Southeast Asia, along with certain parts of West Africa.
A ‘V’ shaped incision is made into the tree. This is called ‘tapping’ and provides a channel for the latex liquid to be drained from the tree and collected. Around 70% of the worlds natural latex is destined for use in tyres.
How did we get here though? It turns out it took a ball game. And a pair of crude rubber boots. Amazonian Indians would make make these from latex. Just how they stumbled upon this discovery, who knows. But it was important. Especially to a young Charles Goodyear who had quite the rubber fetish. Which is a good thing as he invented something known as Vulcanisation. More on that in a bit. For now, we’re just going to add some acid to the raw latex so it coagulates. And whilst that coagulation takes place... we can take a moment to look at the key ingredients (or elements) of a tyre. We’ll be referring to these during the ‘cooking’.
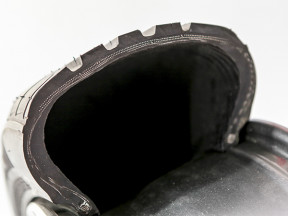
The Tread: It's the Grippy Bit
Let’s start with the bit of the tyre people notice most, the tread. If you have a 4x4, it’s the most exciting part of the tyre tyre too. It says "look at me - I ride over anything I want to". Something like that anyway. Well, the tread is actually made up of multiple sub-components. Namely, the Cap, Base and the Shoulder.
The cap is essentially ‘the pattern’. This is the part that comes most into contact with the road and is responsible for the important stuff... like handling, braking, fuel economy, grip etc. Looks good on a 4x4 tyre too!
Underneath the Cap is the Base. It has a pretty important job too. It needs to protect the Casing but also help to reduce rolling resistance (for improved fuel economy).
The final part of what we consider to be the tread is the ‘Shoulder’. You find this on the... erm... shoulder of the tread, providing the connection through to the sidewall.
Let’s move inside the tyre. The next essential elements are the ‘Plies’. The ‘Steel Cord Belt Plies’ are - your guessed it - thin steel cords that run around the tyre. This is your tyre’s reinforcements and provides the strength and stability to handle highway speeds.
For added stability and handling at high speeds, high quality 4x4 tyres will also have a ‘Cap Ply’. This is usually nylon cord which wraps around the tyre and is embedded in rubber. It sits just underneath the tread.
The Casing: It's the Inside Bit
Some folk with to the casing as the carcass. Which sounds a bit like something vultures pick on, so we’ll stick with casing. The casings main job is to… erm… encase the air inside. By now, you’ll have picked up the naming conventions for tyre elements are pretty simple. So, the casing consists of 3 main elements itself.
First up, we have some rubberised rayon or polyester, known as the textile cord ply. This will control the air pressure in your tyres. Underneath the textile cord ply we find an inner liner. If the job of the textile cord ply is to control the air pressure then the inner liner is it’s best friend. That’s because it’s an airtight layer of rubber which essentially acts as an inner tube.
The last part of the casing is the sidewall. This connects the tread shoulder to the bead. As such, the sidewall needs to be strong enough to repel damage from sharp objects (as well as other things it may occasionally meet, such as roadside kerbs). A well-designed sidewall also plays a part in maintaining ride comfort as well as stability at high speeds.
The Bead: Sticking Tyre to Wheel
Wheels have a small groove or slot. The tyre bead fits in this and is then held in place when the tyre is inflated. Tyres beads have steel at their core, whose job is to make sure the tyre fits firmly on the wheel. A bead apex provides some stabilisation, whilst the bead reinforcement (made of a heat resistant synthetic fibre) aids with steering control and directional stability.
We’ve digressed enough. Let’s move on to how it all gets made and you get a tyre...
The Right Recipe
Of course, rubber is not the only ingredient needed for making a tyre.
We’ll also need a pretty complicated mix of chemicals. There is a bit of an art to this bit too. Actually, it’s all science but manufacturers like Continental have it down to a fine art. They use a proprietary blend of specific chemicals in specific tyres… for… erm… specific reasons. For example one thing that all tyres use is ‘Carbon Black’. Carbon Black is produced by the incomplete combustion of heavy petroleum products such as coal tar. This is used both as a pigment and reinforcement filler in the tyre. Anyone who wants to make tyres can go online and buy this. But the better quality tyre manufacturers will be working closely with their sources of carbon black to ensure they have a reliable supply of all the different grades of carbon black that they require to optimise different tyre features such as handling properties, fuel economy, and damage resistance.
We should also mention silica. You know, the stuff you get in those little packets with new shoes, normally with big bold writing that says ‘Do Not Eat’ (don’t by the way), that’s a form of silica. The stuff in your tyres is a little different and has undergone a chemical modification. Also, it doesn’t come with a ‘Do Not Eat’ sign (still don’t though). Silica is great for wet grip and also improves rolling resistance, so tyre manufacturers often use it along with carbon black. All this good stuff is added to a ‘Banbury Mixer’ and blended together.
What else? Depending on the type of tyres we’re making, we might need some textiles too. The cords used to reinforce tyres can require some rayon, a dash of nylon, a sprinkle of polyester and even a hint of aramid fibre in some instances.
Then we’ll need some steel. But much less than used to be used! If you look at the history of tyres you’ll discover the profession of the ‘Wheelwright’. This labour intensive task was responsible for making tyres from steel. They were moulded onto the wooden wheels of carriages. For us, we just need some for the bead cores and steel belts.
Inside Out
As with all great recipes, you don’t just throw everything into one pot and hey presto - you’ve done it. That only works with soup. Nope, the great recipes for the great dishes require individual mixes and preparation. There’s a process to go through here. What’s more, you need to get it right. As all the best chefs know it only takes one small mistake and the whole dish is ruined. All these food analogies are hopefully making you hungry… or more tyre knowledge, so we’ll power on.
Steel Cord
A tyre is very much made from the inside out. It starts with mixing steel cord and rubber. Or more accurately, embedding the steel cord into rubber so you get a continuous sheet.
Fabric Cord
Elsewhere, much like a steel cord was created, we need to manufacture a textile cord. This is done in much the same way, with the aid of a calender and large roller device to embed the textile into a continuous sheet of thin rubber. It’s a bit like a fancy mangle really. Except it doesn’t just make something flat by forcing it to squeeze through the rollers. It effectively melds parts together, forcing them into one, long joined sheet.
Tread
At the same time, you need to prepare the tread by mixing some of the rubber and shaping it. Like cooking, the secret is in the measurements used as it needs to be an exact weight (as measured in a per metre basis).
Bead
A continuous steel wire, covered by rubber and wound around with several continuous loops, is used to make the required tyre bead. This is the edge of the tyre that sits on the wheel.
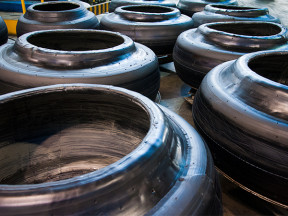
The Green Tyre
All these various parts now need to come together. You’ll need a tyre machine for that. Specifically, you’ll need what’s known as a Tyre Building Machine. It’s a bit like a giant industrial thermomix. Well, not really. But it is pretty neat and it does a great job of taking the ‘ingredients’ and making something with them.
What it makes is known as a green tyre. Whilst it would be kind of fun, a green tyre is not actually green. It’s just uncured. For now it’s time to really get cooking…
Things Are Heating Up
The problem with latex is it goes brittle and can snap when its cold. When too warm, it gets sticky and smelly. Imperfect like this, it would actually be pretty useless for a tyre. That’s the issue early inventors had with rubber. It was just too imperfect to be used to much. That is, until Charles Goodyear (he with the aforementioned rubber fetish) comes into it. We’ll digress a little here, because the story is quite fascinating. Also, Charles was quite the character and started his pursuits in rubber while imprisoned when a former creditor had him arrested. It would not be Charles’ only problems of the financial kind.
The rubber industry in the USA at the time (early 1800’s) was coming to a sticky end. Lots of rubber products were found to be unsuitable because issues experienced when too cold or too warm. Charles was having none of this and worked on a solution. Finally, in 1839, he stumbled upon the idea of adding sulphur before cooking the rubber. It worked.
Getting a patent proved to be a little difficult though. Charles had sent some of the rubber to a few people who had reverse engineered his discovery and taken patents out ahead of him. One was a British chap by the name of Thomas Hancock. It was a friend of Thomas’, one William Borckenden, who invented the term ‘vulcanisation’ from the Roman gods of Fire.
We digress too much (but before we leave Charles... he sadly died penniless. The Goodyear Tyre company you know today has never had anything to do with Charles or his family, it was simply named in his honour). Right then… Vulcanisation. This is when, for a specific period of time, pressure and temperature, the rubber is cured to make it stronger. In essence, the long chains of molecules in the natural rubber are reinforced by sulphur, which has the effect of adding extra bonds or cross-links in the molecules. Sort of like trusses in bridges. The resultant ‘vulcanised rubber’ has almost none of the issues associated with cold and hot temperature variables.
Quality Checks
What we have now is a proper tyre, ready for final quality checks. This means it needs to stand up to a visual inspection but also to an x-ray machine. This is an important step as it you need to be able to ‘see inside’ the tyre to check for any imperfections. Tyre imperfections can have serious (read: grave) consequences, as was the case a few years back when Bridgestone/Firestone recalled 6.5 million tyres.
Only once the quality checks have been completed will the tyre hit the road (figuratively speaking) and make it on the way to your local tyre store.
So there we have it. It all starts with a sticky liquid from a tree. You throw in some steel, textiles and chemicals. Cook and shape. Check and dispatch. How tyres are made really is rather fascinating. Just wait until you learn how the humble garden hose led to a chap named Dunlop to get involved…
But for now, let us give the last word to poor, penniless Charles. You see, Charles was quite philosophical about it all. He also makes a very fine point: Life should not be estimated exclusively by the standard of dollars and cents. I am not disposed to complain that I have planted and others have gathered the fruits. A man has cause for regret only when he sows and no one reaps.
Useful Reference Sites:
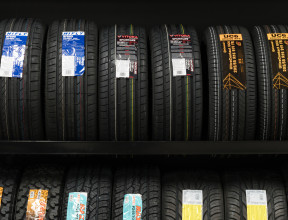
Time for 'New' Tyres?
-
Topics:
- Tyre Technology
More tips and articles
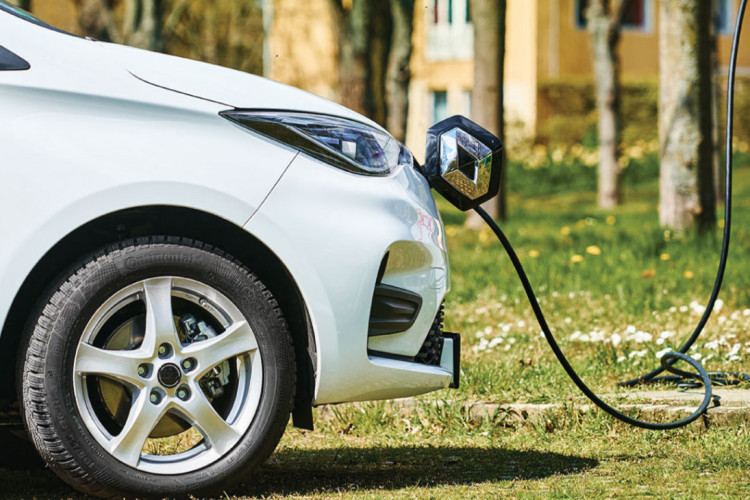
Tyres for Electric Vehicles
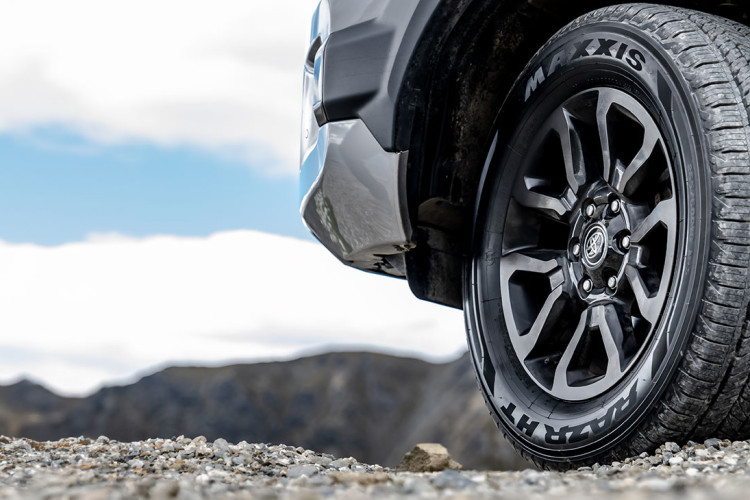
Product Spotlight:
Maxxis HT780 RAZR HT
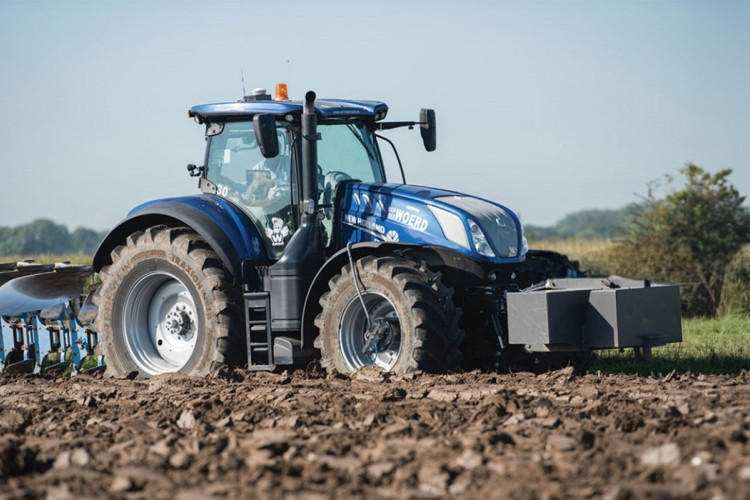